Optimization strategies for Tailor Rolled Parts in car bodys
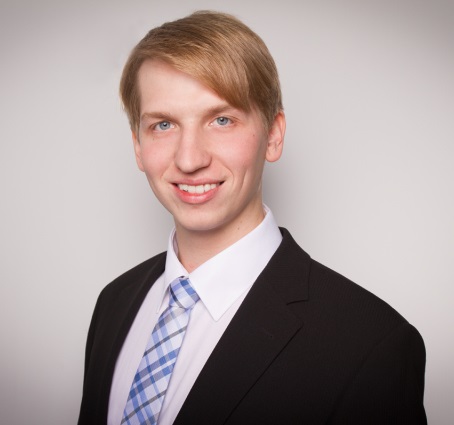
Design space restrictions and complex requirements of modern modern car body
structures lead to sheet metal parts which are rarely fully stressed. The use of
flexible rolled material enables light weighting by decreasing the sheet thickness
in areas, which are less loaded. The production of such material is characterized
by technological constraints and economical specifics. Because of the increased
design freedom as well as the complex relationship between function, cost and
manufacturability the design of tailor rolled parts is time demanding and thus
cost intensive.
This thesis presents strategies for the design and optimization of flexible rolled
parts that make it possible to incorporate function, cost and manufacturability
assessment into a multidisciplinary optimization process. The underlying
calculation procedure allows the formability evaluation based on a technology
specific finite-element-modelling and enables to carry over the influences of the
forming process to the functional evaluation. A cost model is presented, which
respects the economic specifics of the tailored rolling process chain.
The integrity of the passenger cabin must be guaranteed in the case of an accident,
which is why crash load cases have to be taken into account in the design phase.
Since their calculation is time consuming, they determine the turnaround time
of the optimization. The formulation of the degrees of freedom or rather the
parametrization of the thickness run has significant influence on the number of
calculations needed. A clever parametrization enables an efficient optimization,
respecting the technological constraints as well.
Based on the optimization scheme a strategy is developed, which enables the
selection of those parts, whose production from tailor rolled material guarantees
cost-efficient light weighting.
Shaker Verlag, ISBN: 978-3-8440-7936-4