Topology Optimization of Components
The topology of a component, e.g. the position and arrangement of structural elements can influence the structural behavior fundamentally. A topology optimization must therefore be carried out in a very early stage of the design process. The current procedures provide design proposals based on a few given requirements such as allowable design space, boundary conditions and loads.
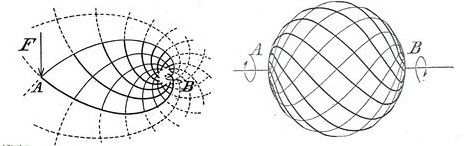
Literature:
Michell A.G.M. (1904): The Limits of Economy of Materials in Frame Structures.
Philosophical Magazine, Series 6.Vo. 8. No 47, 589-597
First Optimization: Michell-Structures (1904)
The topology optimization started with the consideration of truss like structures. Michell has developed a design theory in 1904 in which the mechanical structures are characterized in that their trusses intersect with a 90° angle. This is an optimum arrangement in the sense of maximum tensile and compressive stresses.
Pixel-/Voxel-Method
Procedure:
1. Definition of the design space,
2. Creation of a finite element model,
3. Definition of design variables: For each finite element is to be decided whether there is material or not.
4. Formulation of the optimization problem: Minimize the mean compliance while maintaining a weight constraint
5. Optimization loop (using analytical gradients of the objective and constraint functions in accordance with the design variables)
6. Interpretation (if solution is not practicable: Back to step 3,
7. Generation of a CAD model.
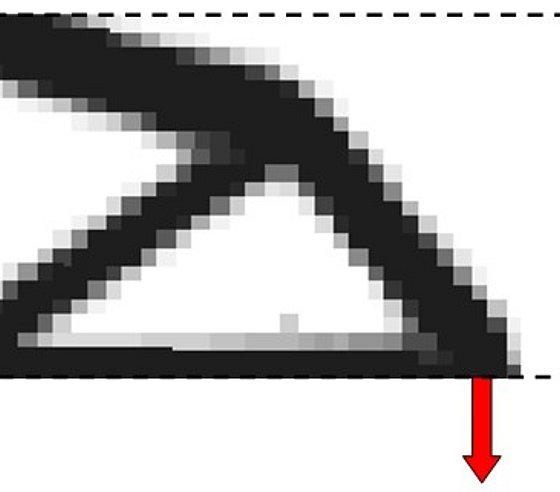
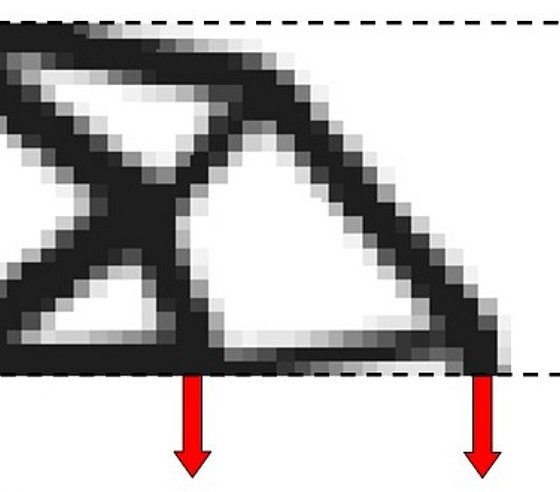
The kind of objective and constraint functions used in the pixel/voxel method are limited, and often do not correspond to the real engineering functions. The results provide only a design proposal which could be highly misleading. Already the simple 2D examples leave a lot of room for interpretations and discussions.
In the pictures optimal topologies for different load application points are shown. The individual loads in the figures are combined. In all cases, the mean compliance is minimized considering a given weight constraint. This weight has always the same value.
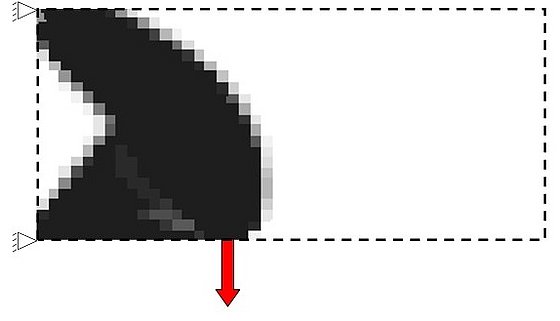
The optimizer uses the maximum allowable weight:
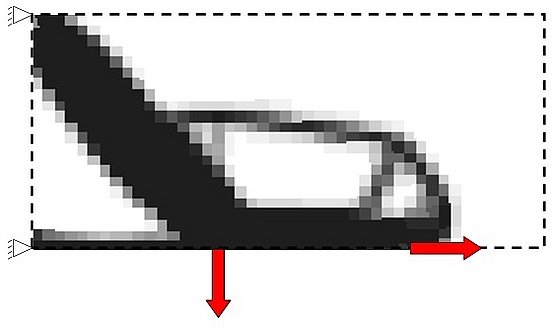
The bar at the bottom left of the fixing point develops so thin because one force creates tension and the other force creates compressive stress. This cancels each other out.
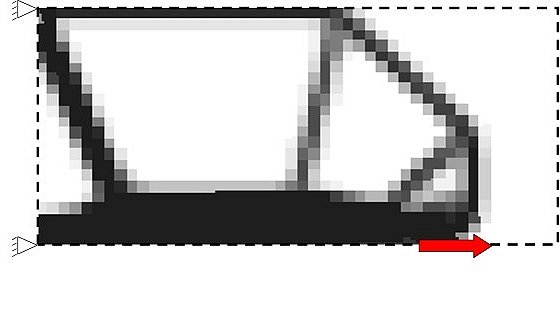
Due to limited design space at the bottom of a supportive structure at the top of the design space developes. Ideal would be a simple tension bar at the bottom. However, it cannot develop centrally to the force, because of the design space definition. Bending deformations arise, which are supported:
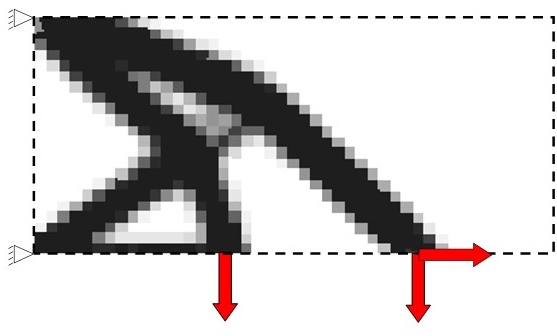
The two orthogonal forces have a resultant 45° downward to the right, so that corresponding 45°-bar develops. This result is absolutely unacceptable for practical components. A small change in one of the two forces would result in a strong bending stress.
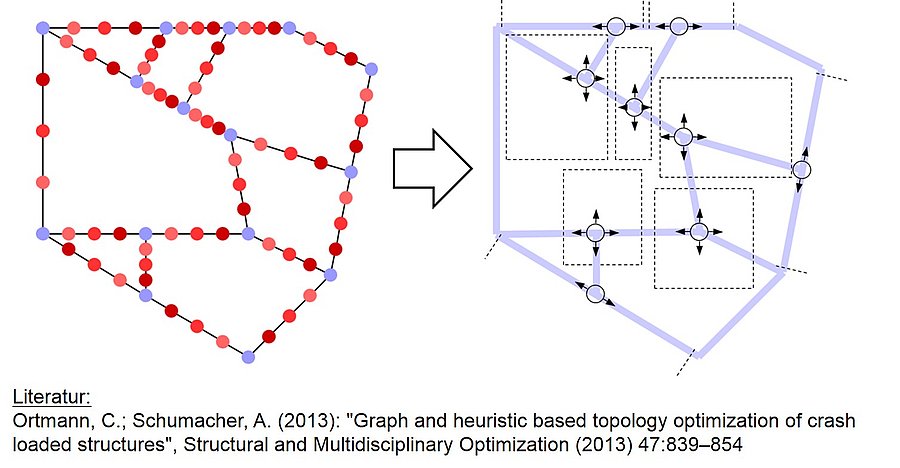
Graph and heuristic -based topology optimization
The graph and heuristic based method uses the real objective and constraint functions. Especially for optimizing crash structures that is important. Based on a mathematical graph a producible crash structure is created in each iteration. In comparison with the pixel/voxel method no analytical gradient calculation can be performed, so that the computation time is much higher. The advantage is that the optimizations are very close to the tasks.
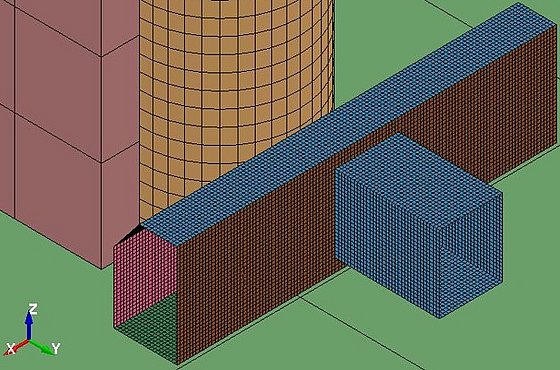
Application:
Find the optimal topology and shape of the profile of a vehicle rocket
Objective function: Minimize the maximum force to the pushing, rigid wall, so that stiffness and manufacturing constraints are fullfilled
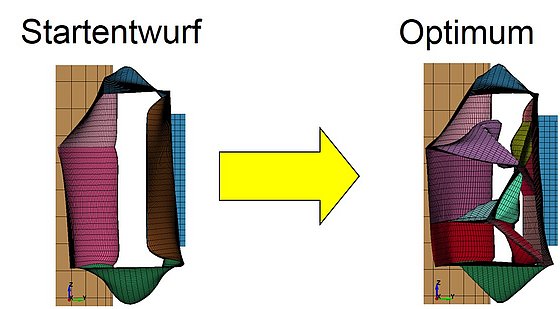
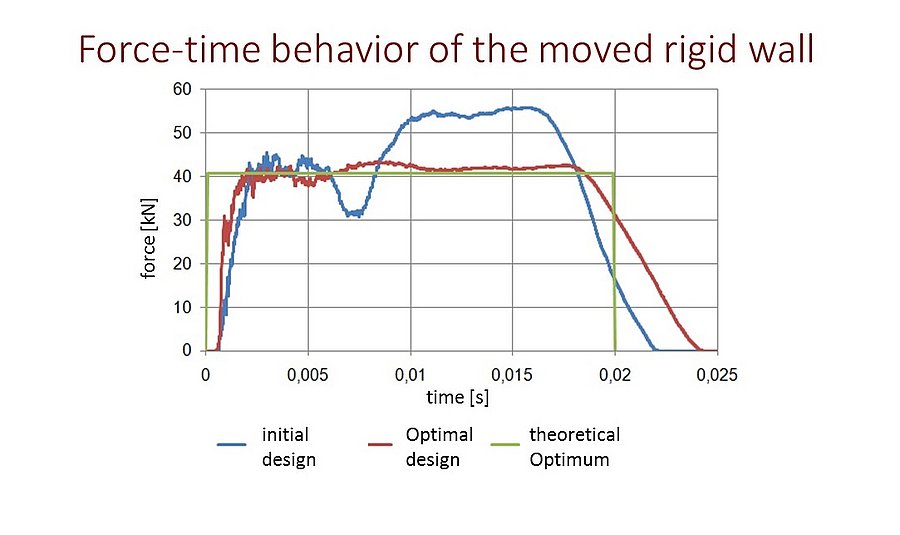
Redesign of a Brake Anchor Plate through Topology Optimization
by Dominik Schneider, with Hypermesh und Optistruct