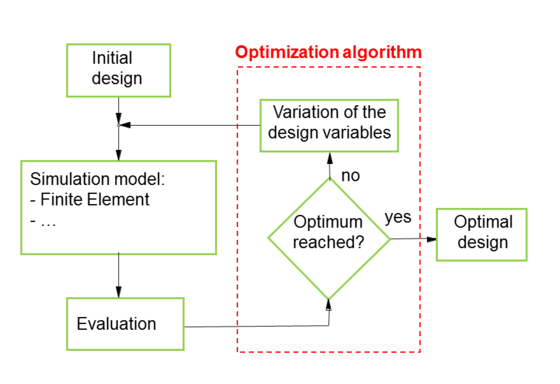
Optimization Loop
As various as the optimization problems are so are the used software programs. In order to choose a program, several tests, but also inquiring the knowledge of other users who have used this specific software already successfully is necessary. Ideally, tips and tricks in terms fo handling the software get exchanged in user groups.
Components get "manually" developed by analyzing the calculated properties and changing the design according to such. This is often very time-consuming, as normally several iterations are needed. The automatic component optimization integrates the simulation sequence into an optimization loop. The chosen optimization algorithm changes the defined design variables and identifies the optimal design. By using a specification list objective and restriction functions as well as design variables get as completely as possible defined.
Important: Considering the Scattering of the influence Parameters
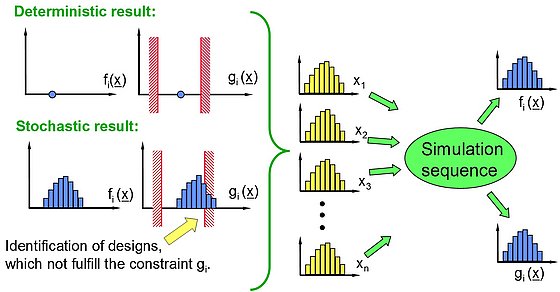
Optimization algorithms often find solutions which cannot be found "manually".
However, it might be the case that solutions found are not robust. The slightest modification of the parameter deteriorates the properties fundamentally. The scattering of the parameters (material properties, load cases, wall thickness etc.) get therefore directly considered in the optimization. Such lead to robust results.
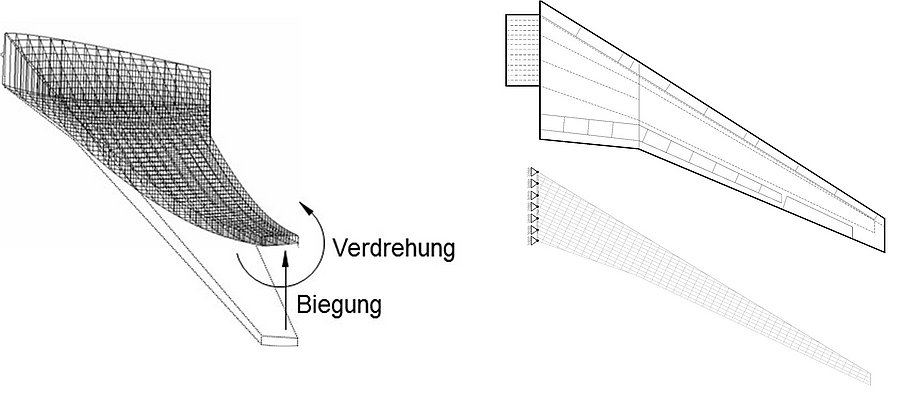
Application Example: Optimization of the outer Wing of an Aircraft
During a long flight the weight changes through the fuel consumption. Hereby also the deformation of the wing changes and is with such not any longer optimal. By using carbon fiber the change of the twisting of the wing shall be minimized, so the wing gets always aerodynamically optimally blown. The design variables are the thickness and the angles of the carbon fiber layers in eight areas. The weight of the wing structure shall hereby not increase.